-
Powder Coating Spray Booths
all-categories-powder-coating-spray-booths
-
Batch Powder Spray Booths, Non-Recovery
These floor model booths make efficient use of shop space and are designed for batch powder coating with no provisions for powder reclamation.
Air is drawn in through the open front of the spray booth, passes through the booth’s working area into the filtered exhaust plenum. The air is filtered in three stages and discharged back into the room. One set of filters will be provided with each booth.
• 1st stage – blanket style filter
• 2nd stage – bag style filter
• 3rd (final) stage – final pleated filter
-
Batch Powder Cartridge Collectors, Recovery
PURGE CONTROL
This feature assures the safe operation of the coatings enclosure, by maintaining the airflow at design levels. During operation overspray powder accumulates on the cartridge filters. As the cartridge filters load, airflow decreases and negative pressure rises within the air handler. A timer activates a system of air purging valves that clear the cartridge filters of accumulated powder to ensure maximum filter life.
-
Batch Powder Booths, Recovery
PANELS
Panels are fabricated from 18-gauge prime quality galvanized steel, flanged and precision punched on 6" centers for maximum rigidity. Panels are fastened together with 5/16" grade 5 bolts and are to be sealed with the provided caulk following assembly.
ILLUMINATION
Lighting is provided by Class I Division II, 48" long, fluorescent, 32 Watt, T-8 type fixtures (four-tube), mounted behind safety glass; appropriately sealed from the interior of the spray booth. All fixtures are UL listed and approved for their intended use and placement.
PURGE CONTROL
This feature assures the safe operation of the coatings enclosure, by maintaining the airflow at design levels. During operation overspray powder accumulates on the cartridge filters. As the cartridge filters load, airflow decreases and negative pressure rises within the air handler. A timer activates a system of air purging valves that clear the cartridge filters of accumulated powder to ensure maximum filter life.
-
EZ Pass-Thru Powder Booths, Conveyorized
Parts enter the booth through the conveyor openings, then pass the coating operator stations to receive the coating. The powder overspray is entrained within the air stream moving to the collector module, where the cartridge filters will remove the particulate. The containment air is drawn through the air handler’s primary and final filter system before being discharged back into the room. Coated parts exit the booth for conveyance to the cure oven.
CONSTRUCTION
Cabin panels are fabricated from 18-gauge prime quality galvanized steel, flanged and precision punched on 6" centers for maximum rigidity. Panels are fastened together with 5/16" bolts/nuts and are to be sealed with the provided caulk following assembly. The base frame and floor support are fabricated with 4" channel and 10 gauge mild steel. Base will ship assembled, and cabin will ship knocked-down for field assembly. #304 stainless steel panels are available as an upgrade.
CONTROL EQUIPMENT
• NEMA 12 Remote Electrical Panel
• Primary Disconnect
• Automatic Purge/Pulse Control
• Main Air Line Disconnect
• Magnahelic Pressure Gauge
Certifications
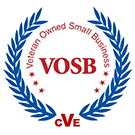
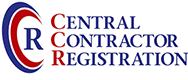

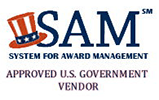